Two years ago, Kim Conley was testing new track spikes for New Balance, and she was skeptical. New Balance’s engineers had taken data about her landing patterns, fed it into a state-of-the-art software program, and then used a 3D printer to tailor five different designs specifically for her running style. All of which sounded intriguing, but Conley, an Olympian and two-time US champion, wasn’t convinced. “To be totally honest, I wasn’t sure how much I’d be able to feel a difference with the finished project,” Conley says. Track spikes, after all, aren’t meant to be noticeable—they’re supposed to do their job and let elite racers focus on winning.
Then she started training in the prototypes. One pair stood out right away. “They had a snugger fit, and gave more traction,” Conley says.
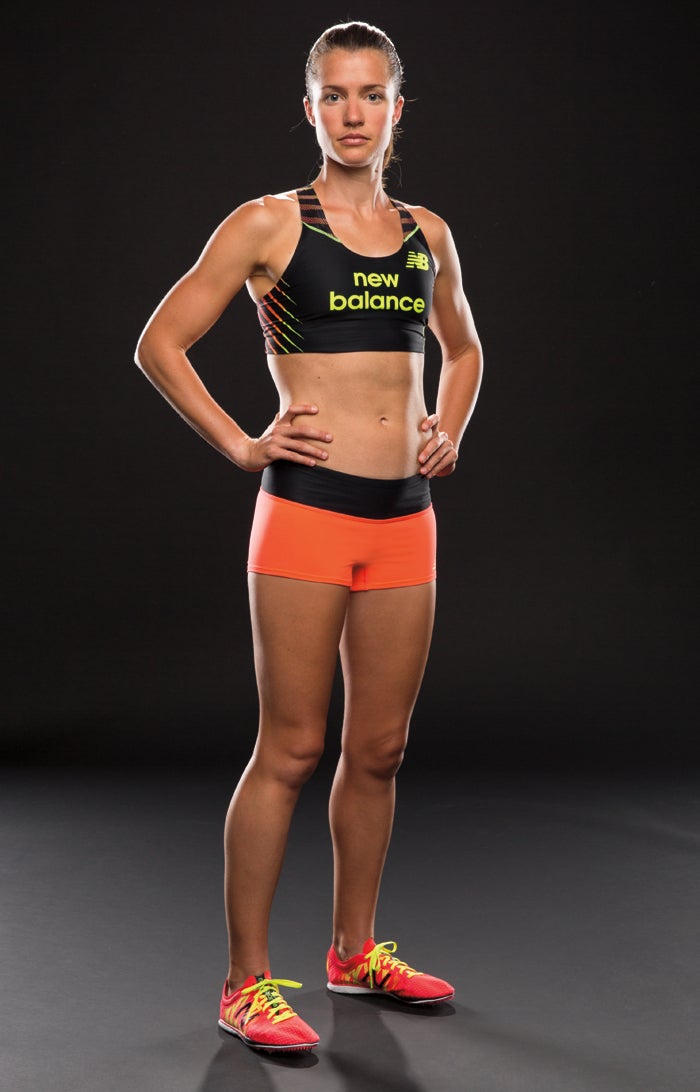
A few months passed, and Conley qualified to race at the World Track and Field Championships, in Moscow. Shortly before the meet, Sean Murphy, who heads New Balance’s Sports Research Lab, asked Conley which shoes she planned to wear for the race. The same prototypes that she’d been wearing for six months, she responded. “We were like, are you kidding, you still have those?” Murphy says. The shoes weren’t meant to last more than a few workouts, but Conley had been using them for months. In fact, she wouldn’t wear anything else. “It was a really good moment for everyone who worked on the project,” Murphy says. It meant that the engineers’ ultimate goal—learning whether there was a new way to build shoes—was working.
Of course, most people don’t wear track spikes. They run on pavement, trails, gravel paths—they need running shoes. Buoyed by the success of their new data to design process, as it became known, Murphy and his team immediately wondered if they could use the same tools to build a better shoe for everyday runners.
But before they could begin designing, they needed more data. And that meant more—and different—test subjects. They didn’t need to look far: New Balance, as you might imagine, has an uncommonly fit staff, and dozens of the company’s employees run at lunch time. Murphy and Trampas TenBroek, a biomechanist who works with Murphy at the Research Lab in Lawrence, Massachusetts, started hanging around the lobby, catching runners as they headed out the door.
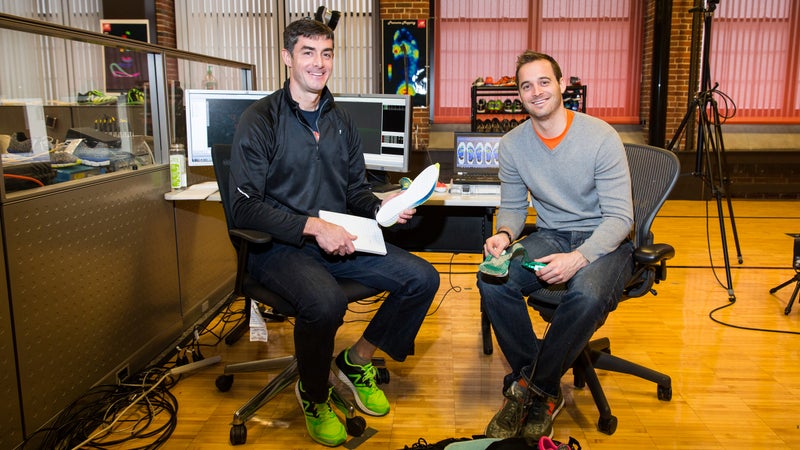
Getting volunteers into the lab was the easy part. Gathering the data proved trickier. Tenbroek and Murphy needed the runners to land squarely, without breaking stride, on a force plate, a 16 by 16 glass plate with a sensor underneath—which is harder than it sounds.
Fortunately, Tenbroek and Murphy had plenty of tech to make up for the inevitable botched landings: wafer-thin sensors inserted into the bottom of runners’ shoes, a set of high-speed cameras, and tiny reflective balls pinned to the runners’ shoes, to track foot position. Put together, Tenbroek and Murphy were able to capture thousands of pieces of data from each stride—and a super-slowed-down picture of what was happening in the milliseconds after the runners struck the ground.
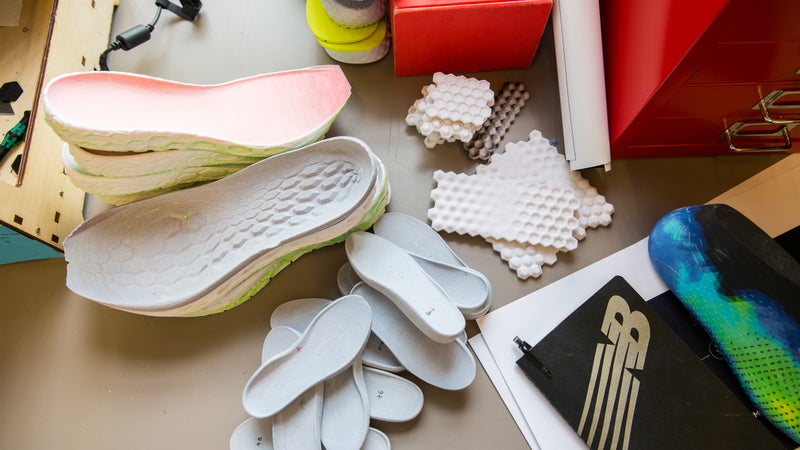
The pair saw a pattern emerge almost immediately. One group had a cluster of high landing forces around the front of their feet, and barely registered any data elsewhere. The second group had a more even distribution, with forces peaking as they landed on their heels, then rising again as they pushed off at the balls of their feet. Now that they had the necessary data, lead designer Chris Wawrousek could do his thing.
Wawrousek is part of a small team at New Balance, called the Studio Innovation Group, which tackles bigger, higher-concept projects. For several years, he’d been preoccupied with a powerful architectural design program named Grasshopper. Now, based on the success of the track spike program with Conley and other elite athletes, and armed with all data from the footstrike study, Wawrousek finally had all the tools necessary to use Grasshopper to see in real time how the midsole reacts to different runners in different conditions. “The beauty is that when I change a detail, I don’t need to go back and change the whole design—I can visualize it in real time,” he says.
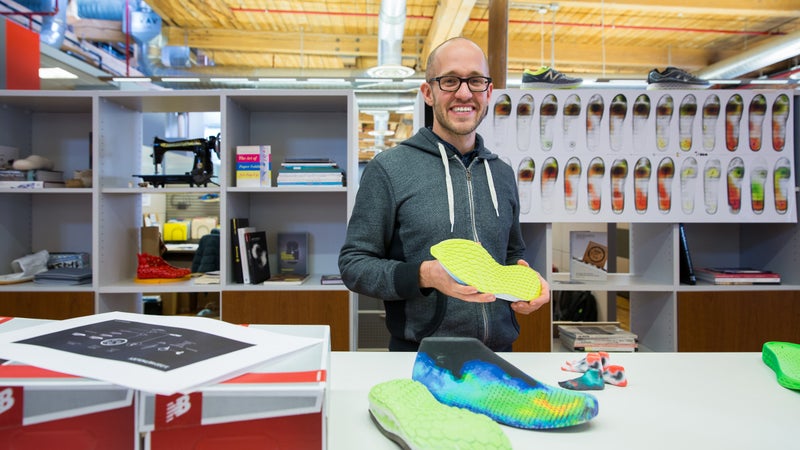
For the first time ever, Wawrousek and his team had an almost unlimited ability to fine tune the midsole. Using the software as a guide, the engineers were able to add and remove the amount of foam in certain areas to create the exact feel they wanted.
You can now see—and experience—the results. In early 2015, New Balance unveiled the Fresh Foam Zante, for the first group (efficient forefoot strikers) and Fresh Foam Boracay, for the second (heel-striking runners). And that’s just the start. The success of the data to design process has spurred other departments at New Balance to begin working with Wawrousek’s software. Up next? The company isn’t saying, but if the stuff looks anything like the new Fresh Foam shoes, it’s gonna be cool.