The scissor jacks that come with most new cars, trucks, and SUVs are woefully inadequate. Relying on one risks your own safety and damage to your vehicle, and could leave you stranded due to a problem as simple as a flat tire. But speciality off-road jacks can also be dangerous, expensive, challenging to use, and difficult to carry. Luckily, there’s a better option.
The Trouble with Scissor Jacks
Look behind or under your rear seat, or inside or underneath the trim in your cargo area, and you’ll probably find a piece of folded metal the owner’s manual claims is capable of lifting your car. The scissor jack your car comes with is designed to interface with specific areas of the pinch weld underneath your doors or vehicle’s frame.
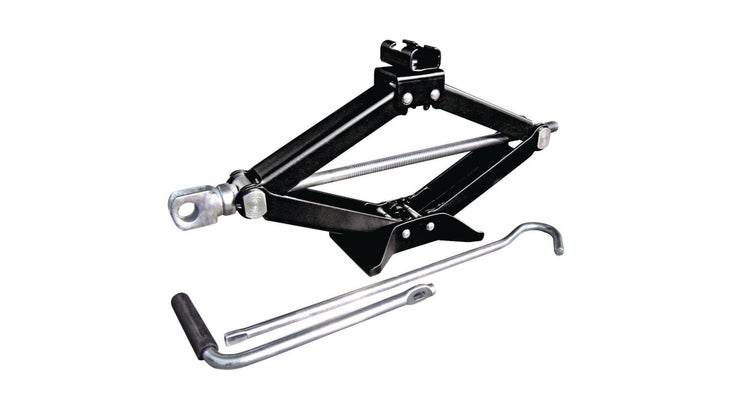
When car manufacturers design or select a scissor jack, they prioritize cost, packed sized, and ease of carry. That’s to say: they’re made to be carried, not used, and target the bare minimum level of function. The weight capacity of that scissor jack hiding somewhere in your car likely tops out at your vehicle’s unladen weight—no more. That means you’re going to have to exert significant physical effort using one to lift even a totally empty vehicle. And that problem is exacerbated by the need to lift from areas of your vehicle above the suspension. Because you must lift from the body or frame, you have to lift the vehicle beyond the travel of its suspension to get a wheel off the ground. And that creates real danger, because scissor jacks are not stable, especially when fully extended.
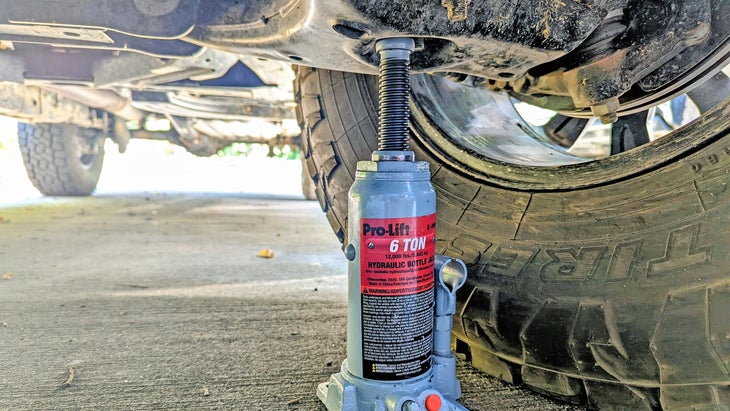
Lift from the Lowest Possible Point
The key to lifting a big, heavy vehicle on an unstable surface is to do it from the lowest point possible, as little as possible. On independent suspension (all cars, the front wheels on most new trucks), that will be the control arms. On solid axles (the rear wheels on most trucks), that’ll be the differential housing or a point on the axle close to the wheel you’re trying to lift (if you have a flat tire).
Because you’re compressing rather than extending the suspension by lifting it, and not the entire vehicle, you only need to raise the jack a few inches to get a wheel or wheels off the ground. This provides stability, reduces effort, and increases safety.
This approach is one of the things that makes the popular hi-lift style of off-road jack the wrong choice. Those are designed to interface with aftermarket bumpers or other protection parts, and because you’ll typically only find them on highly-modified trucks that also have lifted suspension systems, you’re going to have to use a hi-lift jack to raise the vehicle sky high just to get a wheel off the ground. Throw in a loose surface, or one that’s not level, and the hi-lift creates an unstable situation, a problem that’s made more dangerous by the device’s tendency to flap its long steel handle with great speed should the vehicle fall.
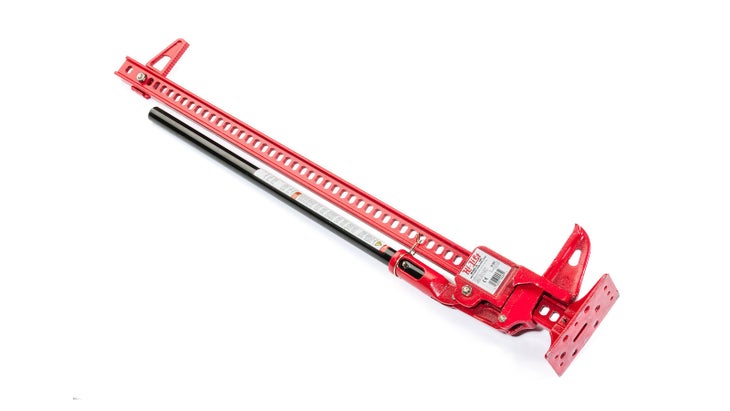
Why Mechanical Advantage Matters
Mechanical advantage is the difference between the force you put into using a jack and the lifting force it produces.
Scissor jacks employ a screw. That’s one of the simplest ways to multiply input force, and also makes it less likely that the weight of the vehicle will reverse the jack’s direction. But it also requires a lever, which is why you have to rig up the jack’s handles into a T, then laboriously spin them around to both raise and lower the vehicle.
The mechanical advantage in a hi-lift is a simple lever. The longer the lever is, the more it will multiply the force. It’s also one of the things that makes hi-lifts dangerous. If the pins that hold the vehicle’s weight don’t engage, the weight of the vehicle acts on that lever, flipping it back and forth with multiplied speed. If the lever hits you, it can kill you.
Inside an hydraulic jack, you use a lever to exert pressure on a small cylinder of incompressible fluid. This flows through a one-way valve, exerting pressure on a larger cylinder. Because the fluid is incompressible, the movement of the larger cylinder must match that of the smaller one. The difference in size between the two cylinders provides the mechanical advantage, and the length of the lever you use to pump the small cylinder helps, too. Thanks to the one-way valve, the weight of the vehicle cannot reverse the jack’s direction, and even if the valve fails or you open the release valve, the small piston does not exert forces on the lever. The presence of that release valve also means you don’t need to work the lever to lower the vehicle.
Because hydraulic jacks employ two forms of mechanical advantage, their levers can be short. And because they’re built to lift under a vehicle’s suspension, so don’t need to extend to a huge amount, the jack itself can be made very short too. That makes them easy to store, and easy to position under a control arm or axle—even with a totally flat tire.
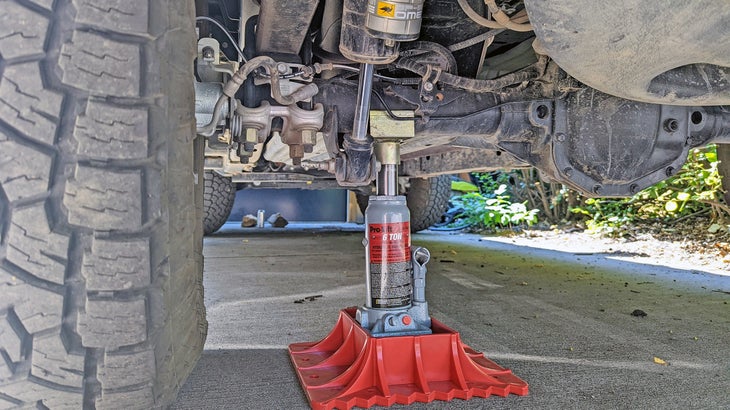
Which Hydraulic Jack Is Best for You?
A bottle jack is a hydraulic jack in its simplest form. It’s just that big and little cylinder, base, ram, and lever.
What’s the right capacity Six tons, or 12,000 pounds, will be one-and-a-half to two times the maximum loaded weight of most passenger trucks or SUVs. That margin will make operating the jack on a six- to eight-thousand-pound vehicle as easy as possible, while still giving you a compact device that measures just eight-and-a-half inches tall. Sizing up may give you a stronger jack, but comes at the cost of added height that could make it challenging to fit under suspension supporting a fully deflated tire. (Drivers of crossovers or other cars equipped with small tires may be better served by a two-ton bottle jack, which measures just seven and one-eighth inches in height.)
Most six-ton bottle jacks appear to be made on the same pattern. Whether you buy it from a big box store, a discount tool retailer, or on the Internet, the only difference appears to be the label and color. The cheapest brand I found was Pro-Lift, . If you can find one for less, buy it.
And this thing is already proving its worth. Twenty miles into a very rocky off-road trail the other night, after dark, I heard a clanging sound from my front suspension. Pulling over into a vaguely level patch of dirt, I grabbed the bottle jack out of , stuck it under the control arm, and had the vehicle safely lifted by about an inch, plus my wheel off and under the front cross member, in about 90 seconds. Turned out I’d lost the nut that connects my sway bar end link to the driver’s side spindle. Without a replacement nut, I removed the end link entirely, and drove on home. My total delay? Maybe ten minutes, and both my truck and me were safe the entire time. I used the same jack to reinstall the end link and add a new nut in my driveway the next day.
An important safety note from the author: Never rely on the jack alone to support a vehicle once lifted. At home, use a quality pair of jack stands to support the frame. In the field, position your spare tire, or something similar, underneath the frame close to where you’re working so that if the vehicle falls, it falls on the tire. Before using your jack, place four-wheel drive vehicles in four-low and park (automatic transmissions) or first gear (manuals). On two-wheel- or all-wheel-drive cars, ensure the vehicle is in park (automatics) or first (manuals). Apply the parking brake on all vehicles. Chock the wheels on the axle you’re not lifting to prevent them from rolling away from the axle you’re working on.