In Sakai City, on Japan’s Osaka Bay, I watched blacksmith Jun Mizuno forge raw steel into polished blades as fierce and honed as swords. He does it the way his father and grandfathers taught him: heating billets of raw jigane iron in the fire, burning powdered hagane steel into it for strength, then hammering the alloy by hand until it’s sharp and smooth. It’s the same method blacksmiths in this port city used for centuries to craft weaponry for the samurai and part of a broader smithing tradition, including guns and tools, that has earned Sakai a reputation for precision metalwork.
Shimano, which crafts some of the finest metal bicycle components on the market, also hails from Sakai City. Last week, I had the chance to visit the company’s factory for the launch of Shimano’s new top-line mountain components, XTR 9100.
How Shimano Builds Components
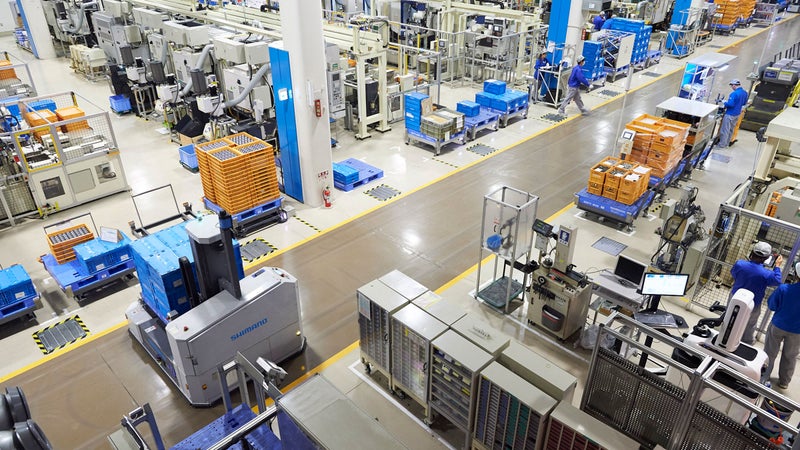
The factory floor, bigger than six football fields, is incredible to behold, especially when you consider that it accounts only for Shimano’s highest-end bike products, XTR and Dura Ace, as well as some fishing equipment. (Lower-tier parts are built elsewhere in Japan, as well as southeast Asia.) Shockingly, from a catwalk above the floor, I could only ever see a dozen or so people monitoring and working at the machinery. Production is mostly accomplished by robotic arms and conveyor belts, and unmanned forklifts drive containers of parts from station to station.
Production of an XTR crank starts with sheets and tubes of aluminum. The process consists of five steps: forging, in which the metal is pressed into shape; machining, where precise shapes like spindle holes are cut away; heat treating, where the temperature of the metal is raised and cooled to add strength and rigidity; surface treatments, such as anodization, for durability; and gluing, with laser guiding that creates seals so precise they are virtually invisible.
There are variations on all of these processes. For instance, cold forging is used for three-dimensional objects such as brake calipers, while hot closed-die forging, where the metal is heated and then injected into a form, is best for complicated shapes such as brake levers. Every new or updated component requires fresh molds and sometimes new machines, each of which can take six months to a year to develop.
It’s been four years since Shimano came out with the previous-edition XTR group set, XTR 9000. The company says it took all that time to get the new group right. Dozens of people, including several engineering teams, a dedicated industrial designer, and three product managers, went back and forth to field feedback from dealers and consumers, decide what technological advancements to include in each component, hit weight and performance targets, and home in on the look and feel.
Then came two years of prototyping and testing, with countless iterations of each component and the complete group. The final XTR 9100 prototypes were produced in December 2017. Mass production commenced May 14; if initial samples pass quality control, full production will start on July 1, with delivery to consumers sometime in the fall of 2018. “It’s a huge process, much bigger than I think people really understand,” said Nick Murdick, Shimano’s mountain bike project manager for North America, at the 9100 unveiling. “This is the day I’ve been waiting for. It’s not really real until you put it out to the public.”
The Nitty-Gritty: XTR 9100
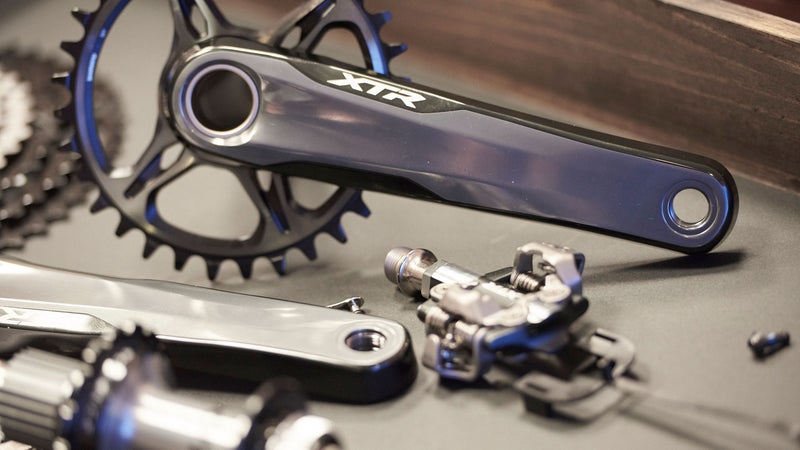
The biggest change to XTR 9100 from the previous edition is the jump from 11-speed to 12. At last, Shimano introduces a wide-range cassette, 10- to 51-tooth, which gives it an even bigger range than SRAM Eagle, though the company will also offer 10- to 45T options in both 11- and 12-speed setups for those favoring lower weight or tighter gear steps, respectively. The range of choices keeps in line with Shimano’s desire to cater to all riders; it also reflects XTR’s bisection into both cross-country and enduro racing. (There will even be a 2×11 option, though Shimano admits the market is negligible.)
Other changes are nuanced technology developments, most notably Hyperglide+, which smooths out shifting by reshaping gear teeth and redesigning the chain so the tolerances are tighter. Shimano says this removes the clunkiness when shifting down the cassette so that moving to a bigger gear feels as seamless as moving to a smaller one. The crank is now direct-mount, which alleviates proprietary spider configurations, and a new free-hub technology eliminates splines so freewheeling is silent. Brake levers are completely revamped with a new bracing point to improve rigidity and control, and a new enduro-specific pedal adds stability and contact area for sneaker-styles shoes. There’s even a slick dropper-post lever, the company’s first, with ergonomics inspired by its substantial shift-button know-how. Finally, as always, overall weights are down.
All that technology won’t come cheap, though Shimano slots in below the competition. An XTR 9100 drivetrain in the XC setup (crank, 10- to 51T cassette, chain, shifter, rear derailleur) will retail for $1,254, compared to $1,356 for SRAM Eagle XX1. XTR brakes (levers, calipers, hoses, and rotors) will go for $760 complete versus $720 for SRAM Guide Ultimates.
Shimano has been on the back foot in mountain bike components for a few years, not because the previous iteration wasn’t a great product, but because the Japanese manufacturer was slow to adapt to consumer enthusiasm for single-ring drivetrains, while SRAM fed it. “I loved XTR 9000, and Di2 was effectively a 1×13 system because the front derailleur did the shifting for you. But it just came at the wrong time, because it wasn’t where the market was,” Murdick told me. “I think you’ll see that 9100 puts us back at the top of the game.”
Having lagged behind in mountain bike development, Shimano needs a hit with the new XTR, which may be part of why the company has made such a big deal about the release of 9100 despite the relative subtlety of its improvements. In the end, the new components made me think of Mizuno and his knives. Off the shelf, any good kitchen knife will be sharp, but the fastidious construction process and attention to detail is what (supposedly) makes Mizuno’s superior. In an effort to reclaim its mountain bike mantle, Shimano is making the same argument about XTR 9100.
The new components look promising. But it’s impossible to say for sure until I get my hands on a group for long-term testing—which is in the works for next month—because the proof, of course, is in the ride.